A Comprehensive Guide to Precision and Efficiency
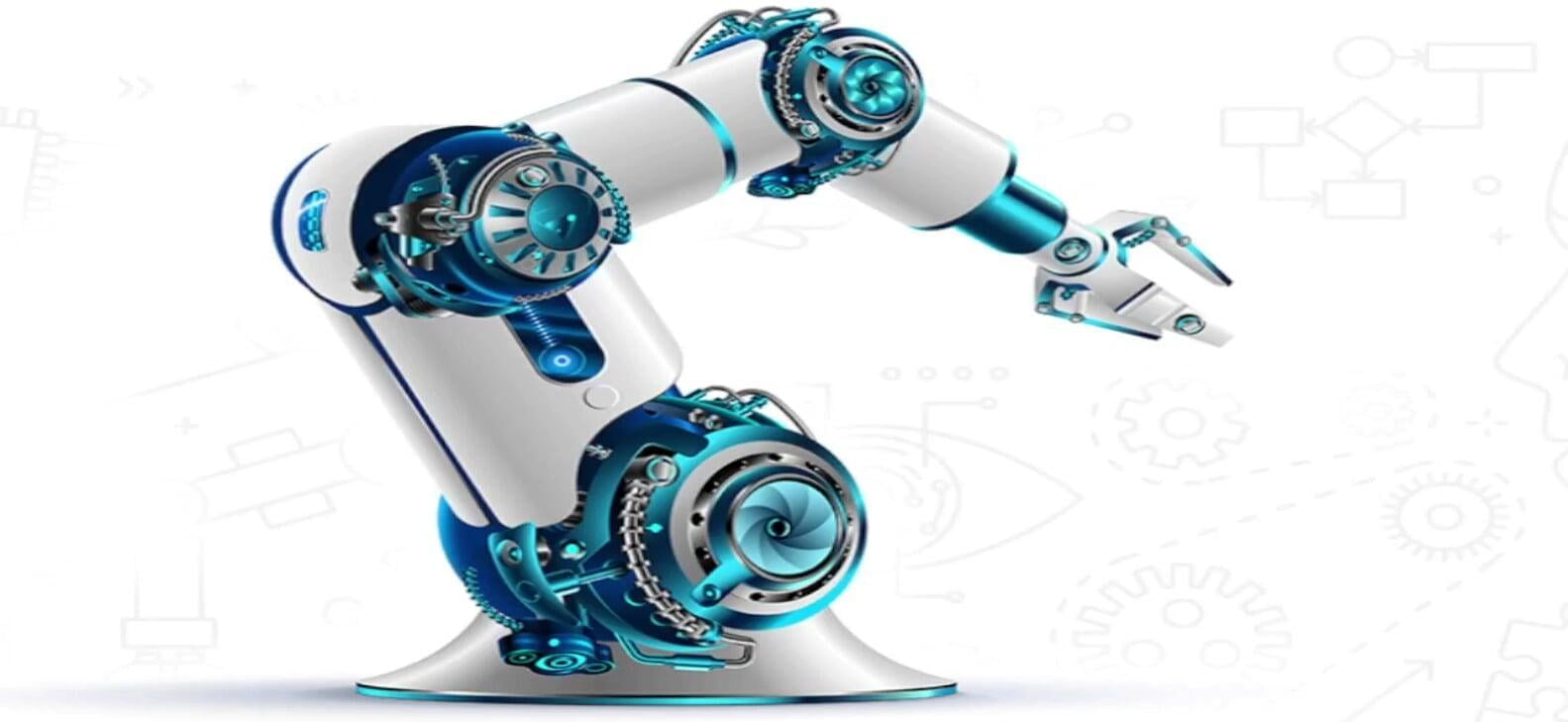
INTRODUCTION
Efficiency and accuracy are essential for success in the ever-changing field of industrial robotics. One of the many tasks carried out by robots is arc welding, an essential application that supports the manufacturing processes of numerous sectors. The establishment of a Tool Center Point (TCP), a crucial reference point that determines the exact place where welding activities are done, is essential to the smooth execution of robotic welding jobs. We explore the complexities of TCP development for arc welding torch robots in this extensive book, outlining the methodical procedure, stressing the significance of appropriate tool selection, and showcasing the detailed methods for defining tool frames. Manufacturers may raise production and keep a competitive edge in the market by improving the accuracy, effectiveness, and dependability of their robotic welding processes through the mastery of TCP development.
UNDERSTANDING TCP CREATION:
The Tool Center Point (TCP) is a fundamental notion in robotic programming for arc welding. The robot is guided to carry out welding maneuvers with the highest level of precision and accuracy by the TCP, which acts as a crucial reference point. The TCP essentially marks the precise location of the interaction between the welding torch and the workpiece, guaranteeing structural integrity and constant weld quality. Manufacturers can increase total productivity and profitability by optimizing welding operations, minimizing mistakes, and maximizing throughput through careful TCP definition.
IMPORTANCE OF PROPER TOOL SELECTION:
It is crucial to stress the significance of appropriate tool selection before starting the TCP building procedure. The choice of tool has a major impact on the precision, effectiveness, and dependability of operations in robotic welding applications. A mismatched or inadequate tool can cause incorrect positioning, weld flaws, and production delays, all of which can compromise the robotic system's overall performance. To ensure smooth integration and best performance, great thought must be paid to selecting the proper tool that matches the specific requirements of the welding process.
DEFINING TOOL DATA:
Creating a TCP requires a careful description of tool data, which includes dimensions, weight, the center of gravity, and orientation, among other crucial aspects. Precise robotic operations require reliable tool data, whether it is created or imported from a predetermined tool. Manufacturers can allow precise simulation, motion planning, and trajectory development by giving the robot extensive knowledge about the tool. This reduces the likelihood of errors, collisions, and inefficiencies during operation. Furthermore, appropriate tool data guarantees robotic system compatibility and permits smooth coordination between the robot and welding torch, improving overall system dependability and performance.
A STEP-BY-STEP GUIDE TO TCP CREATION:
1. TCP Pointer Import:
- Choose a world-fixed tip in the robot's workspace to act as the TCP pointer to start the TCP construction procedure.
- Insert the TCP pointer into the robotic workstation, making sure that it is oriented and aligned correctly for the welding torch and the workpiece.
2. Modifying TCP Pointer location:
- Align the TCP pointer with the workpiece or the fixture table by adjusting its location to ensure accurate placement for upcoming operations.
- Adjust the TCP pointer's location using the workstation's graphical user interface, keeping ergonomics and space limitations in mind.
3. Choosing the Tool:
- Make sure the tool is compatible with both the robotic system and the welding task by selecting the appropriate one from the workstation's tool library or dropdown menu.
- When choosing a tool, take into account many aspects such as its weight, centre of gravity, mounting arrangement, and geometry to achieve maximum dependability and performance.
4. Defining the Tool Frame:
- Determine the tool frame's orientation, elongators, and mounting configurations by creating a reference point in the world coordinate system.
- Make use of the tools and utilities available at the workstation to precisely define the tool frame while keeping the welding application's and the robotic system's requirements in mind.
5. Setting Tool Parameters:
- Establish critical characteristics for precise motion planning and simulation, such as tool weight, a centre of gravity, and inertia qualities.
- Enter exact numerical values for the tool parameters while considering the tool's physical attributes and how it interacts with the robotic system.
6. Creating Approach Points:
- To ensure ideal positioning for welding actions, specify approach points for the TCP by combining circular and linear motions.
- Use the motion planning tools on the workstation to create the robot's smooth and effective trajectories, reducing cycle time and increasing throughput.
7. Verifying and Finalizing:
- Before beginning any welding activities, ensure the calculated results are accurate and reliable by confirming the formation of the TCP.
CONCLUSION:
In conclusion, Mastering the creation of a TCP for an arc welding torch is indispensable for achieving precision and efficiency in robotic welding applications. By meticulously following the steps outlined in this guide, manufacturers can optimize their robotic workflows, ensuring seamless operations and impeccable output quality. With proper tool selection, precise definition of tool frames, and meticulous attention to detail, mastering TCP creation becomes a cornerstone of success in the realm of robotic arc welding.
Additionally, by employing advanced simulation tools and virtual environments, manufacturers may conduct comprehensive testing and validation of the TCP generation process, ensuring seamless integration and superior performance in real-world applications. Using industry best practices for TCP generation enables businesses to stay ahead of trends, meet changing consumer needs, and foster innovation in the robotic welding sector.
Join us at CNCTRAIN to delve deeper into robotic welding and other CNC, Robotics Courses and Simulation tools for enhancing your technical skill and your knowledge.
Our products and services are suitable for institutions, students, organizations, and individuals who utilize tools and software for robotics and CNC machines, specifically for controlling, simulating, and operating machines. Whether you are part of a team or working individually, we offer many software and tools or tailored solutions to meet your specific needs. We also offer many E-learning Courses or Onboarding Courses for many professions like Mechanical Engineer, Electrical Engineer, Electronics Engineer, Mechatronics Engineer, Automation Engineer Digitally Twin Engineer, and Robotics Engineer.
1. For Individuals: Take advantage of free e-learning and standalone or solo licensing to reach your full potential. Take advantage of job-role-based classes, internships, and more. Begin your journey with us right now!
2. For Institutions: Use e-learning that is tied to the AICTE and bulk licensing to empower your instructors and students. Engage in real projects, internships, and customized assessments. Avail a free one-week trial now!
3. For Businesses: Boost creativity in your smart manufacturing business with technology-based e-learning and bulk licensing. Benefits from onboarding programs and job role-based assessments can help your workforce become more skilled. You can get a week's free trial on your request.
Please sign up by clicking here to receive notification of more details, and further product and service offerings. And do follow us on LinkedIn and Twitter as we take you on a path to become an expert in TCP creation and to further your industrial robotics career. Learn more quickly and take advantage of fascinating chances in cutting-edge technology. Enroll today to experience manufacturing's future with us and don't miss out! and if you have any questions or need assistance, our dedicated support team is always available to help.