Introduction
In previous blog we discussed evolution, history, uses, application, types and anatomy of robots. So let us go ahead, When we imagine robots, we often bring to mind sci-fi-inspired, humanoid machines. While most of these devices are still fictitious, there are a variety of other robots in use today. But, foremost, what exactly are robots? And how will they effect global change? Many of us are comfortable with the basics of robots, but we may find it hard to distinguish them from other kinds of technology. As per our earlier conversation in a previous blog, robots are machines that can perceive, think, plan, and act on their own. They cannot only accomplish jobs on their own, but also enhance human skills and emulate human actions.
About
Robotics is the study of how to build robots. It is a various disciplines that bring together computer science, engineering, and technology. Experts work on the design, manufacture, operation, and use of robots in a variety of settings. Robots can work in hazardous conditions for humans, for as with hazardous chemicals or in high-radiation zones.We already discussed the anatomy of robots in previous blog so.In this blog we will continue with robots in Industry and the anatomy of robots and how many types of Industrial robots are present based on anatomy. Now,We will also explore some other things related to robots.
Robots in industry
Robots have revolutionized the industrial workplace since their arrival in the industrial field. Most of the robots do accurate tasks and fall into then categories.
Arc welding- In the 1980s, arc welding (also known as robot welding) became popular. One of the main reasons for transitioning to robot welding is to protect workers from arc burns and toxic gases.
Spot welding- Spot welding combines two contacting metal surfaces by passing a significant current across the spot, melting the metal and forming the weld in a short amount of time (approximately ten milliseconds).
Material handling- Robot used to move, pack, and select products, material handling.
Machine tending- Machine tending includes loading and unloading raw materials into machinery for processing, as well as monitoring the machine while it performs its tasks.
painting- Robotic painting is utilized in the automotive industry and many other industries to improve product quality and accuracy.
Picking, packaging and palletization- Picking and packaging by robots improves speed and accuracy while cutting manufacturing costs.
Assembly- Robots commonly construct things, removing time-consuming and exhausting processes. Robots boost productivity while lowering costs.
Mechanical cutting, grinding, Deburrig and polishing-Robots with dexterity provide a manufacturing option that would otherwise be impossible to automate.
Gluing, Adhesive sealing and spraying.
Other processes including Inspection, Water jet cutting and soldering.
Anatomy of Industrial Robots
Robot anatomy deals with the study of various joints and links and alternative aspects of the manipulator's physical construction. Anatomy of six axes vertically articulated robots divided into two sections with different functions.
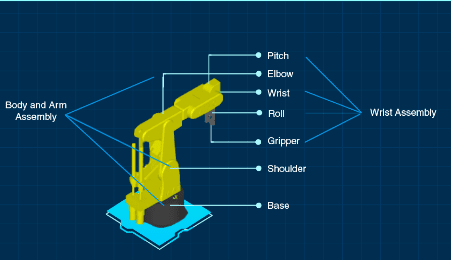
Anatomy of Robots
Robot anatomy deals with the study of different joints, links and other aspects of the manipulator's physical construction. There are some types of industrial robot based on anatomy.
SCARA 4 axes robot-SCARA (Selective Compliant Assembly Robot Arm) robots with four axes provide a circular work envelope with a wide range of motion for increased versatility. SCARA robots have a four-axis design that mimics the action of a human arm.
Five axes mini robot-An articulated robot is a five-axis robot. A robotic manipulator is attached to a rotating base in its configuration, which is common
of industrial robots.
ARISTO 6 axes robot- ARISTO is a 6-axis articulated robotic arm that can carry a payload of 2.5kg. Pneumatic or vacuum grippers are available for ARISTO.
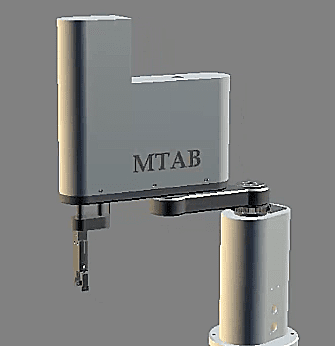
Types of Robots
Robots can be classified into two types:
1.Base Robots
(i) Fixed base robots (ii) mobile robots
2.Body and arm assembly
(i) Cartesian robots.
(ii) Cylindrical robots.
(iii) Spherical robots
(iv) SCARA robots
(v) Articulated robots
(vi) Parallel robotsWrist assembly of robots
Each robot wrist assembly has two or three degrees of freedom. Typical three degree-of-freedom wrist joints in the below picture.
The roll joint is accomplished by use of a T-joints.
A second R-joint is used to achieve the yaw joint, which provides right and left motion.
The pitch join is achieved by recourse to an R-joint.
Frames in Robotics
A frame or coordinate system defines a plane or space by axes from a fixed point called origin.Robots targets and positions are located by measurements along the axes of coordinates system
A robot uses several frames or coordinate systems,each suitable for specific types of programming.
Base coordinate system-The base coordinate system has its zero point in the base of the robot,which makes movements predictable for fixed-mounted robots.It is useful for jogging a robot from one position to another.
Work object coordinate system-The work object coordinate system corresponds to the workplace. It defines the placement of the work piece with the world coordinate system (or any other coordinate system).It is defined in two frames-(i) User frame (ii) Object frame
Tool coordinate system- The tool coordinate system has its zero position at the center point of the tool. It thereby defines the position and orientation of the tool.
World coordinate system- The world coordinate system has its zero point on a fixed position in the cell or station.This makes it practical for managing many robots or robots that are manipulated by outside axes.
User coordinate system- The user coordinate system can be used for representing equipment like fixtures and workbenches. This gives an extra level to the chain of coordinate system, which might be useful for handing equipment that holds work objects or other coordinate systems.
Tool center point (TCP)
The tool center point (TCP) is the point in relation to all defined robot positioning. Usually the TCP is defined as the relative position on the manipulator turning disk. The tool center point also constitutes the origin of the tool coordinate system. Note that the robot system can handle a number of TCP definitions, but only one can be active at any one time.
Two basic types of TCPs are
moving TCP
stationary TCP
Robot control system
Robot sensors measure robot configuration or condition and its environment and send such information to the robot controller as electronic signals
A robot controller's core roles are:
User interface
Data storage
Motion planning
Real-time control of joints' motion
sensor data acquisition
Interaction and synchronization with other machine.
Interaction with other computational resources
conclusion
It is well-known that, dependency on robots is increasing day by day in industrial field. Robotics is the need of the hour in many fields. If you belong to the mechanical and robotics engineering field and you want to start a career in this field. Abhyaz offers a skill development program as well as an internship program where you can obtain more hands-on experience.
FAQs
Q1. How do robots behave?
Ans. Robots are machines with pre-programmed movements that can move in specific directions or sequences.
Q2. What is Robotic Automation?
Ans. It is a method of automation in which a machine acts like a human to complete a task according to a set of rules.
Q3. Which was the first industrial robot?
Ans."Uni mate" was the first industrial robot. It was designed by George Devol, an American inventor, in 1950 and first used in 1954.
Q4. Does the Abhyaz platform provide training for Robotics?
Ans. Yes, Abhyaz provides training as well as internships to obtain more experience.